After a long-term utilization of talc roller mill, the grinding roller and ring will be worn that can be divided into mechanical damage, fatigue damage, thermal damage and chemical damage. Though this low-intensity wear does not only affects the production, it impacts on the service life of the talc roller mill. Then how to solve this issue as a manufacturer?
Maintenance Tips
- Replace the grinding rollers of the talc grinding mill once they have been used over 500 hours, the rolling bearings in the roller sleeve must be cleaned, the damaged accessories and parts should be replaced in time, and the refueling tool can be filled with lube manually.
- Adjust the fineness of the grinding mill. the final fineness can be different according to different size, degree of hardness and softness, moisture content of the talc material. the upper analyzer can be adjusted on the principle of high rotation speed makes high fineness, low rotation speed makes low fineness. This adjustment of talc fineness can both satisfy customer's requirements and protect the roller and rings from being heavy damaged.
- Stop feeding before turning off the talc roller mill, and grind the remaining talc powder material for about one minute, then you can turn off the motor and analyzer of mill, and remember to clean the residual powder.
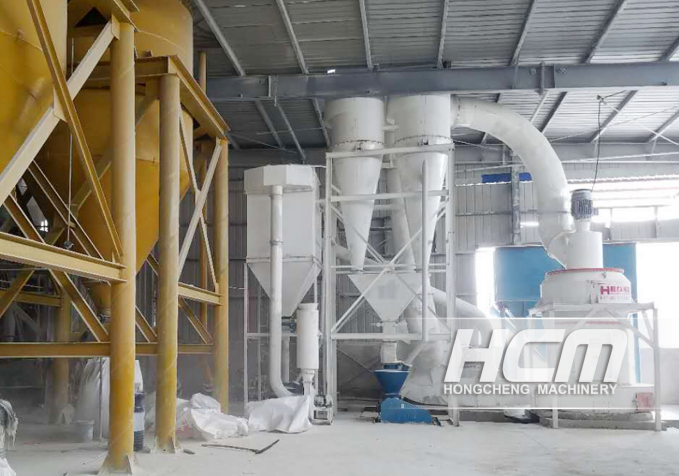
R-Series Roller Mill for Talc Grinding
Hcmilling (Guilin Hongcheng) R-Series Roller Mill is a high efficiency mill used in Limestone, calcite, activated carbon, talc, dolomite grinding. R-Series has been field tested and proven over the years and is widely used to grind minerals with Mohs hardness below 7 and moisture below 6%, the fineness can be adjusted in the range of 80mesh to 600 mesh.
Advantage of Hcmilling’s R-Series Roller Mill
- An increased output of 40%, and saves 30% power consumption cost.
- Fine powder with defined grain size.
- Shock mitigation system can be allocated based on customer’s fineness requirements, more stable and durable performance.